Investment Casting
01
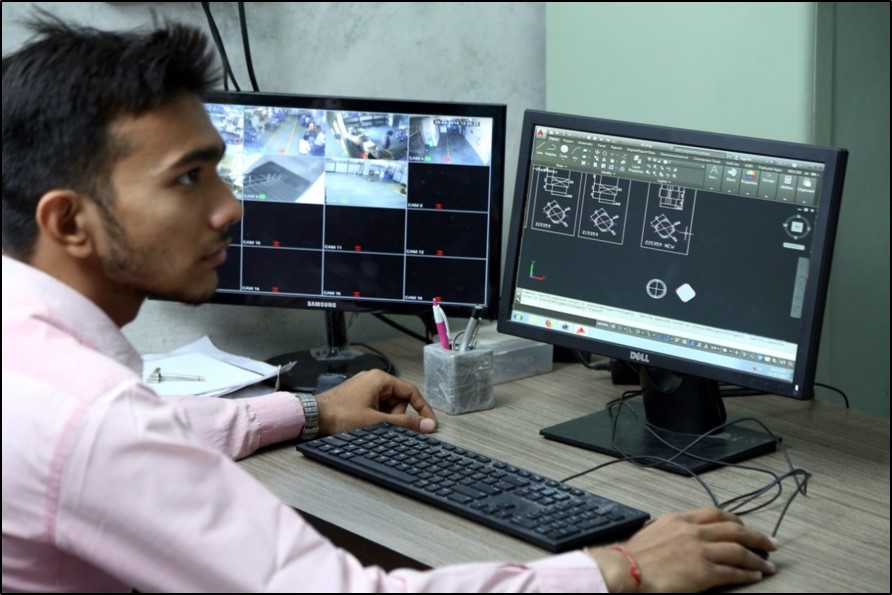
Tool Room
Fully equipped tool room with
- 3D CAD/CAM facility to design tooling as per client drawings/samples.
- CNC Turning and Milling Centers to machine forged aluminum dies for the investment casting unit, wooden and aluminum patterns for the no-bake sand casting unit and cast iron patterns for the shell molding unit as per CAM generated programs.
02
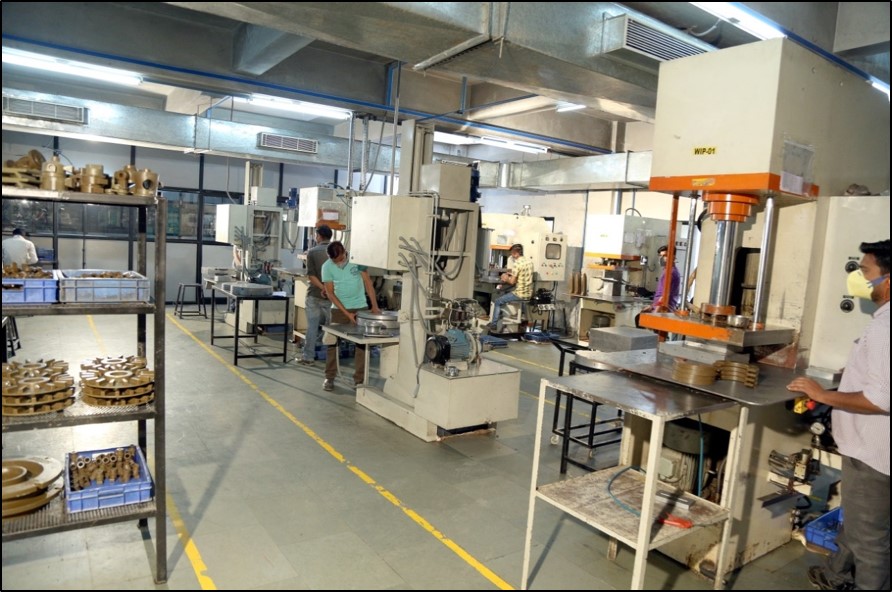
Wax Pattern Injection
Central AC wax injection room with precision temperature control to prevent dimensional variations in wax patterns equipped with
- Multiple auto and manual injection presses with facility for horizontal and vertical injection of patterns.
- Facility to cool automatic injection dies to allow for bulk production.
03
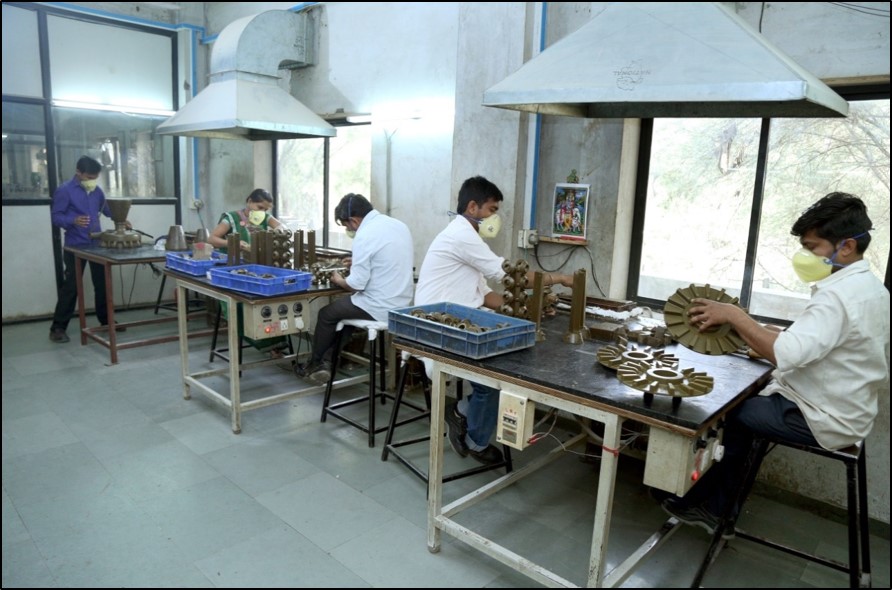
Wax Assembly
A well-ventilated assembly room with multiple assembling stations to assemble patterns into trees as per approved route-cards.
04
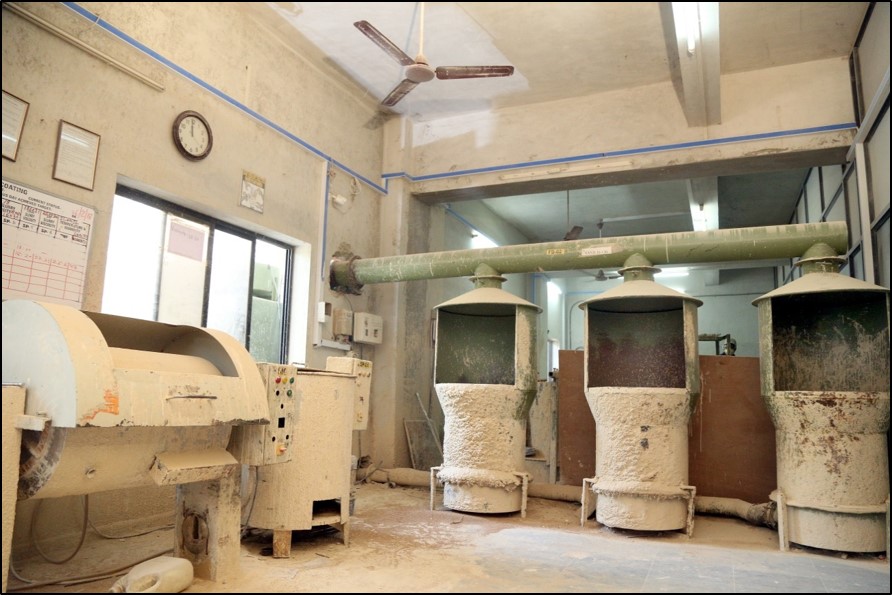
Coating
Separate coating rooms for pre-coat and backup coat application have been setup with
- Various Slurry pots, slurry mixers, rainfall machine and fluidized beds.
- Manipulator to handle large size shells.
- Separate rooms for pre-coat and backup coat drying.
05
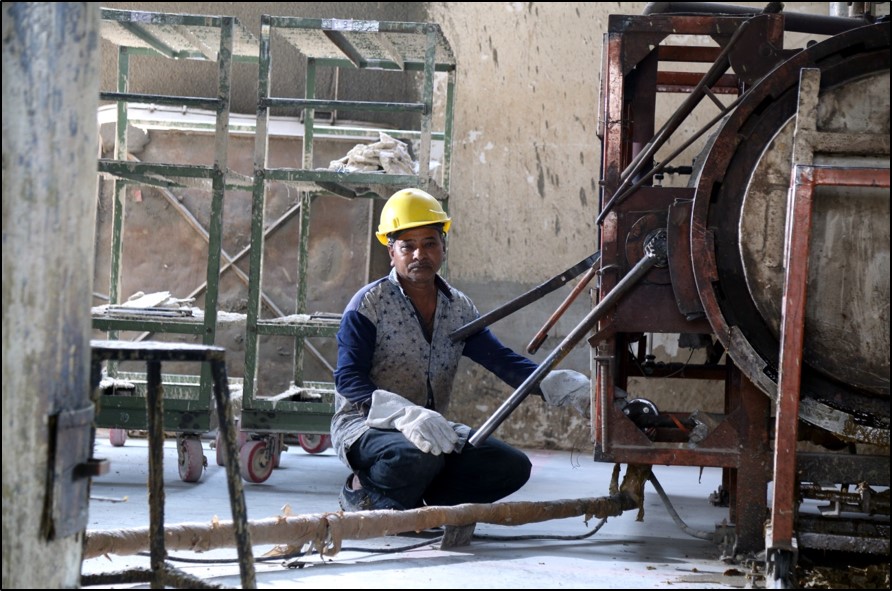
Dewaxing
A shell-type boiler and autoclave for de-waxing of shells without causing cracks.
06
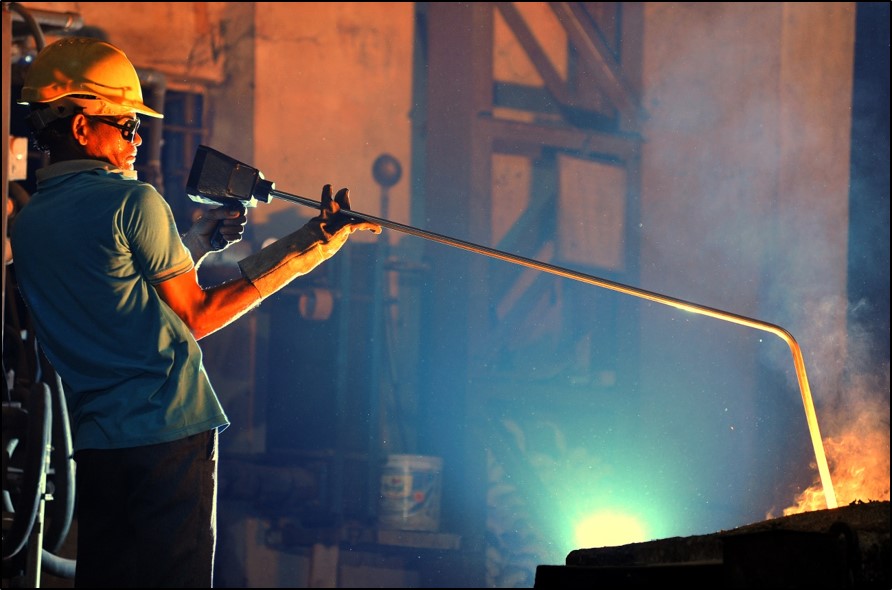
Melting
- Multiple Gas-fired shell firing furnaces to pre-heat shells before pouring.
- Multiple medium frequency induction furnaces (Inducto-therm make) with 300 kg crucibles for melting of scrap.
- PMI machine for effective screening of scrap before loading into furnace
- Multiple pyrometers to ensure right pouring temperature
- CCD based Spectrometer from BRUKER, Germany with capacity of analyzing 27 elements (including Nitrogen).
07
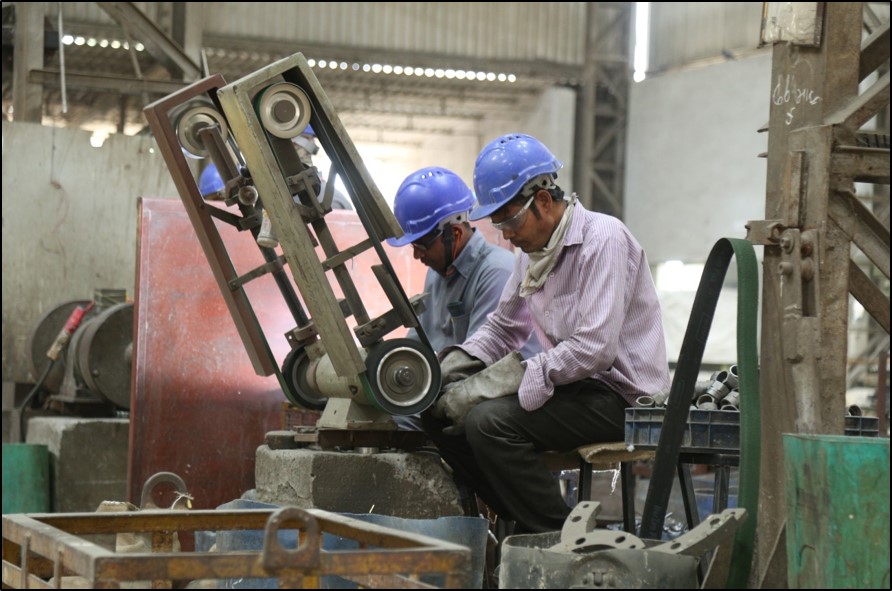
Fettling
Fettling shop equipped with
- Multiple pneumatic knockout machines, heavy duty disc cutting machines
- Heavy-duty bench grinders
- Multiple swing grinders with two stations
- Multiple belt grinders with two stations each
- Multiple shot blasting machines